top of page
機会損失削減による生産性向上
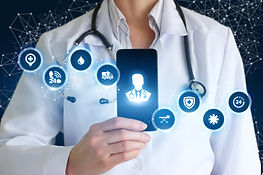
課題
・機器の故障が発生してからの対応となっており、復旧に時間がかかる。
・故障が発生した時にすぐに情報が欲しい。
・不良ロットが絞りきれず、処分や再検査に手間/費用がかかる。

原因分析
・定期メンテナンスだけでは不十分だった。
・故障の予兆となるデータが収集出来ていなかった。
・データに基づくトレーサビリティが取れていなかった。

解決策
・みまわり君により運転データを収集し見える化。
・故障の予兆となる閾値を設け、データによる状態基準メンテナンスを行い、故障が発生する前に
対策を行う。

効果

・故障情報が関係者にすぐに伝わり、復旧までの時間が短縮された。
・チョコ停ドカ停が減り、生産効率が上がった。
・不良が発生しても、機会損失が最小限で済むようになった。
1サイクル30秒、単価25円、8個取りのうち2個不良を
12時間出し、全数点検(1個当たり点検時間5秒)した場合の機会損失
①製品廃棄:1440ショット×2個×25円
= 72,000 円
廃棄個数2880個
②不足分を再生産したことによる機会損失:
360ショット×8個×25円
= 72,000 円
③点検作業費:
1440ショット×8個×5秒 × 人権費1時間当たり6,000円
= 96,000 円
合計 240,000円の機会損失
ゼロに!
導入後
・見える化は以前からやりたいと思っていましたが、何から手を付ければいいのか分からない
ままでいました。導入までの期間が短く、導入費用も安いので助かりました。

お客様の声
・不良が確認されたときに該当ロットを絞れるので、廃棄が減りました。
関連製品
bottom of page